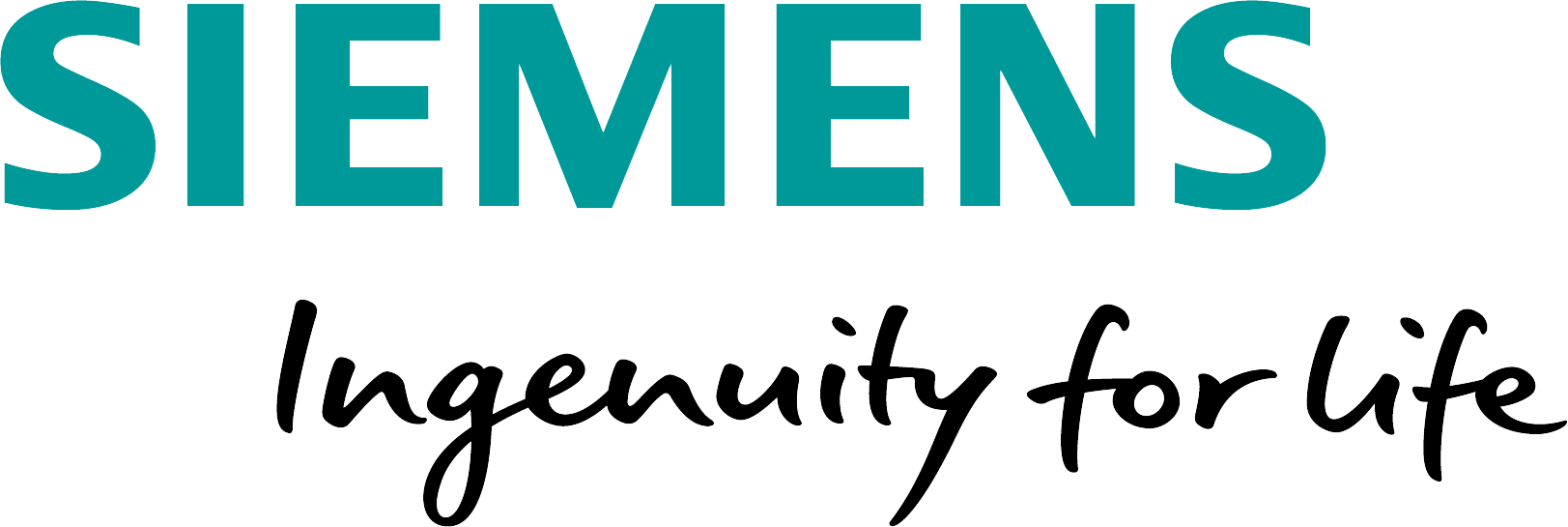
Bringing IoT to the stationary side of rail transportation
Helping Siemens Mobility reduce rail operator’s expenses by looking outside the train
Helping Siemens Mobility reduce rail operator’s expenses by looking outside the train
Railroad operators need digital to improve operations without disrupting their assets or processes.
Siemens Mobility expanded operators’ savings opportunity beyond mechanical installations.
Next Mile helped Siemens Mobility find a connected offering opportunity that imposed a very low change burden on operators:
A digital twin for railroad crossings will give operators the foundation for new insights and capabilities.
For decades, governments and corporations have invested billions of dollars in positive train control (PTC) to increase safety through standardized operation. However, mobile assets are only half the equation—trains ride on infrastructure.
Like many industrial assets, railroad crossings are 30+ year capital investments that constantly change, but never move.
Siemens Mobility knew that modern digital could help address this missing half of efficiency. They invented the electric tram in 1881 and remain at the forefront of transportation efficiency, pioneering advancements in mobility management, electrification, rolling stock, and digital control.
When designing industrial internet of things applications (IIoT) it’s easy to ignore the downstream impact of any decision. Even a simple sensor can impose an untenable change burden in a high-stakes regulated environment. Siemens Mobility knew such a blunt approach wouldn’t work for rail owners, and quickly disqualified every obvious plan.
Siemens had no shortage of ideas, but needed information from the field and external perspective to channel expertise and focus their efforts. Above all, digital technology needed to improve the status quo, not break it. They knew the next steps would be tricky, so they hired Next Mile.
Siemens and Next Mile began by centering on rail customers. We unpacked the state of the industry, revisiting past ideas, reviewing a trove of preparatory documentation, and discussing Siemens’ expert impressions of life as a maintenance of way technician or a logistics expert. From there, we tailored our research plan to address each key audience.
The factory isn’t the obvious place to start a deep customer research effort, but it’s the first place a product meets reality. Siemens manufacturers and engineers held deep knowledge about what their products meant to customers in the long term.
Next, we put our boots on, riding with engineers, sweating with service technicians, and planning alongside logistics experts. Our research uncovered what mattered most to each. When we peeled back context, most raw user needs centered on limiting the time burden of repetitive tasks in over-busy schedules, ensuring access to part locations, and reducing downtime.
At first glance, customers wanted the information provided by a traditional digital twin of the crossing itself. However, Siemens couldn’t instrument a fleet of crossings without asking customers to make a colossal reinvestment.
Next Mile’s independent perspective fully validated Siemens’ previous disqualifications. It felt like we’d arrived at a dead end.
No singular connected product can truly upend 150 years of established process. Technologies must work together against a legitimate need to produce value worth changing for.
When we stepped back, Next Mile’s investigation did illuminate potential users’ real needs. Contrary to early expectations, it turned out that a connected product wasn’t required to deliver what they wanted.
As part of stepping back, Next Mile investigated other available sources of data coming from both Siemens Mobility and railroad operators. While direct, sensor-derived crossing-specific data was still a gap, we noticed that Siemens and railroad operators had that gap surrounded.
That gap was an opening! In many cases, if you know x and you know y, you can derive z accurately. This way, Siemens Mobility will create a digital twin of an analog crossing, but not by instrumenting hardware. Instead, they’ll leverage surrounding context, combining existing and new data sources to synthesize a mirror image of an instrumented crossing without implementing a single in-field change.
Our findings and collaborative ideation gave Siemens Mobility a viable route option to help railroad operators with digital services without upending their operations with massive capital investment.
Siemens moved from thinking about digital as a physical product to thinking about digital offerings. They’ll translate their deep railway management expertise into digitally delivered services, offering as much or more value.
Siemens is a recognized leader in digital twin development and can execute without additional help. They just needed a spark to see customers and connected offerings differently.
By building a digital twin for crossings, Siemens will improve service, reduce risk, and build future value for rail operators and all of us who depend on rail.